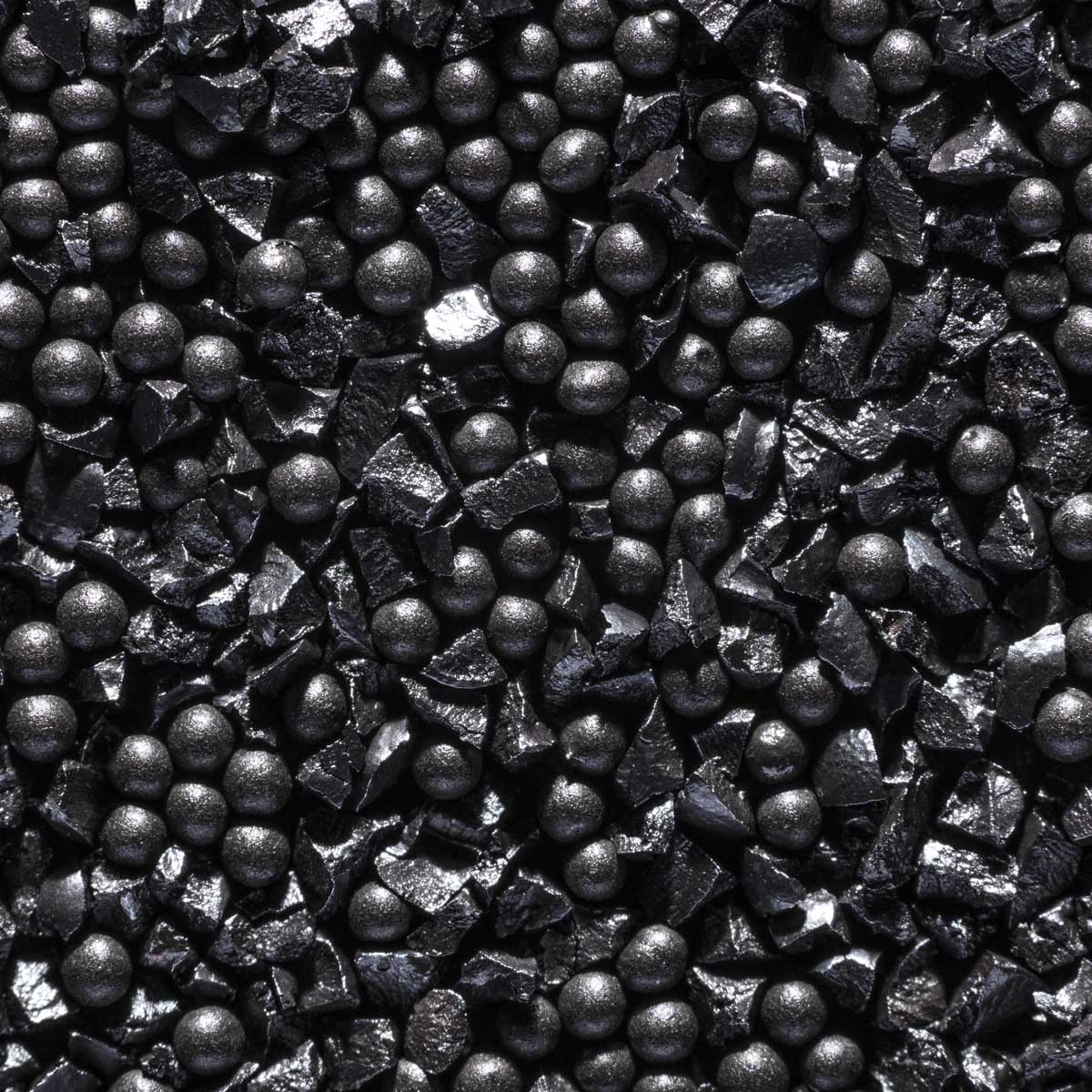
Ideal For
- Automatic wheel blast machines
- Air blast systems
- Desanding, descaling & deburring
- Surface preparation
- Shot peening
- Cutting
Applications
- Foundry and Forge
- Metallurgy
- Transportation
- Energy sector
- Construction
- Fabrication
Some of the key benefits you can expect when using AMASTEEL are:
The Ervin technology for high carbon steel abrasives is the most advanced in the world. We manufacture to third party international specifications in Glaubitz, Germany.
This ensures AMASTEEL shot and grit is a consistently high quality martensitic abrasive. Continuous quality control, in combination with the cutting-edge production process, optimises durability and cleaning power.
Steel abrasive is not a commodity. It is an essential component in a process that can be very costly if not maintained and supported on a regular basis.
Our trained technical support personnel are therefore at your disposal, at no additional cost. We can arrange to visit relevant plants as required on a regular basis to provide:
C | 0.80 - 1.20% | |
---|---|---|
Mn | (S70 to S110) | 0.35 - 1.20% |
(S170) | 0.50 - 1.20% | |
(S230 and above, all grit sizes) | 0.60 - 1.20% | |
Si | 0.40% MIN | |
S | 0.05% MAX | |
P | 0.05% MAX |
S Shot & Grit | 40 - 51 HRC (390 - 530 HV) |
---|---|
M Shot & Grit | 47 - 56 HRC (470 - 610 HV) |
L Shot & Grit | 54 - 61 HRC (570 - 720 HV) |
H Grit | ≥ 60 HRC (700 HV) |
Uniform tempered martensite |
Shot ≥ 7.0 g/cm³ |
Grit ≥ 7.3 g/cm³ |
SHOT | mm | 2.800 | 2.360 | 2.000 | 1.700 | 1.400 | 1.180 | 1.000 | 0.850 | 0.710 | 0.600 | 0.500 | 0.425 | 0.355 | 0.300 | 0.180 | 0.125 |
---|---|---|---|---|---|---|---|---|---|---|---|---|---|---|---|---|---|
SAE | 7 | 8 | 10 | 12 | 14 | 16 | 18 | 20 | 25 | 30 | 35 | 40 | 45 | 50 | 80 | 120 | |
S780 | AP | 85% MIN |
97% MIN |
||||||||||||||
S660 | AP | 85% MIN |
97% MIN |
||||||||||||||
S550 | AP | 85% MIN |
97% MIN |
||||||||||||||
S460 | AP | 5% MAX |
85% MIN |
96% MIN |
|||||||||||||
S390 | AP | 5% MAX |
85% MIN |
96% MIN |
|||||||||||||
S330 | AP | 5% MAX |
85% MIN |
96% MIN |
|||||||||||||
S280 | AP | 5% MAX |
85% MIN |
96% MIN |
|||||||||||||
S230 | AP | 10% MAX |
85% MIN |
97% MIN |
|||||||||||||
S170 | AP | 10% MAX |
85% MIN |
97% MIN |
|||||||||||||
S110 | AP | 10% MAX |
80% MIN |
90% MIN |
|||||||||||||
S70 | AP | 10% MAX |
80% MIN |
90% MIN |
GRIT | mm | 2.800 | 2.360 | 2.000 | 1.700 | 1.400 | 1.180 | 1.000 | 0.710 | 0.425 | 0.300 | 0.180 | 0.125 | 0.075 |
---|---|---|---|---|---|---|---|---|---|---|---|---|---|---|
SAE | 7 | 8 | 10 | 12 | 14 | 16 | 18 | 25 | 40 | 50 | 80 | 120 | 200 | |
G10 | AP | 80% MIN |
90% MIN |
|||||||||||
G12 | AP | 80% MIN |
90% MIN |
|||||||||||
G14 | AP | 80% MIN |
90% MIN |
|||||||||||
G16 | AP | 75% MIN |
85% MIN |
|||||||||||
G18 | AP | 75% MIN |
85% MIN |
|||||||||||
G25 | AP | 70% MIN |
80% MIN |
|||||||||||
G40 | AP | 70% MIN |
80% MIN |
|||||||||||
G50 | AP | 65% MIN |
75% MIN |
|||||||||||
G80 | AP | 65% MIN |
75% MIN |
|||||||||||
G120 | AP | 60% MIN |
70% MIN |
Special sizes are available upon request.
SHOT: SAE J444 & J827
GRIT: SAE J444 & J1993
AP = All Pass
MIN = Minimum
MAX = Maximum
Our sales office can guide you through the quotation process. Please call +49 30 400 37846, visit the contact page or complete the form below.
Ervin can come to your assistance if you require world-class steel shot blasting solutions. Steel shot blasting is the ideal surface preparation method and is commonly used to remove sand, scale, rust, oxide, previous coatings and more. Steel shot blasting goes by many different names and is also referred to as shot blasting and abrasive blasting. The process often takes place in a blast room and automatic wheel machine and can be used to clean, strengthen and prepare metal. Surfaces can also be cleaned with grit before they are coated. Shot blasting is an environmentally friendly option that is used in a wide range of industries including the automobile sector, aerospace, rail and many more.
Steel shot blasting ensures scale, rust and other coatings are completely removed from a surface so new coatings can adhere to the steel. You can expect the coating to fail unless it is added to a clean and properly prepared metal surface. In steel shot blasting, steel is fired against the surface with compressed air or by machine blasting. Steel shot blasting is ideal for cleaning, smoothing and roughing a surface. The shots are delivered at high velocity so the right results can be achieved.
During the process, small particles between 0.125-3mm in diameter are propelled against the surface. The bigger the pellets are, the rougher the surface will be. Opting for smaller shots will give you a smoother and more polished finish. Chilled iron grit can be used for certain metals but is not a suitable match for softer surfaces like aluminium. There are two main shot blasting technologies in use today, and these are wheel blasting and air blasting.
Ervin can help you achieve shot blasting solutions of the finest calibre. We have a century of experience behind us, having been first founded by John F Ervin in the early 1920s. The company remains in the family, and this is just one of many reasons why so many clients and customers choose us when they require shot blasting solutions from a brand they can depend on. We are more than happy to work with you to help you find the right cast steel abrasive (either steel shot or steel grit) for optimal steel blasting efficiency. When designing all of our products, they are carefully monitored to meet international standards and have production centres across Europe and the USA. Our solutions are delivered direct to customers via a robust network of trusted distributors.
When you opt for Ervin steel shot blasting solutions, you can expect to achieve a long-lasting finish of the highest quality. More and more big-name customers are choosing Ervin when they require steel shot blasting solutions. We are very confident that we can help you achieve your aims. We are here to help you meet your steel shot blasting requirements, no matter how complex or ambitious they are. To speak to a member of our sales team today simply give us a call, use our solutions finder or complete the short form on our website.
Amasteel shot and grit is a high-quality martensitic cast steel abrasive for use in blasting machines, air blasting, peening and stone cutting. It is available in a range of sizes and hardness.
In addition to Iron, Amasteel also includes small quantities of Carbon, Manganese and Silicon, to internationally specified (SAE) standards. There can also be traces (maximum of 0.05%) of Sulphur and Phosphorus. A full chemical specification can be found and downloaded on this page.
Amasteel abrasives are available in a range of hardness. Amasteel Shot is available in S,M and L hardness, covering a range from 40 – 61 HRC (390 – 720 HV). Amasteel Grit is available in the same hardness plus there is also a H Hardness; ≥60 HRC (700 HV). Amasteel Shot has a density of at least 7.0 g/cm 3 , Amasteel Grit has a density of at least 7.3 g/cm 3 . A full specification of hardness and densities can be found and downloaded on this page.
The microstructure of Amasteel Shot and Grit is uniform tempered martensite.
Amasteel cast steel abrasives are supplied as either shot, grit or mixes of shot and grit. Ervin has a wide range of standard products, and regularly develops customised product solutions for customers.
Amasteel cast steel abrasives are widely used in automatic wheel blast machines and air blast systems to remove sand, scale, and burrs. It is ideal for preparation of surfaces, shot peening and stone cutting. Amasteel shot and grit is valued in many industries including Foundry and Forge; Metallurgy; Transportation; Energy; Construction and Fabrication.
In both laboratory tests and real-world trials over many years, Amasteel abrasive shot and grit consistently outperforms competitive products delivering the highest productivity and lowest cost solution. Typically, this results in lower consumption, reduced wear and reduced dust and waste disposal for customers. The rigorous adherence to third party international specifications at our manufacturing plant in Glaubitz, Germany ensures a consistent cast steel abrasive that optimises durability and cleaning power. Ervin also offers local technical support to all Amasteel customers to optimise results for customers.
Amasteel is very effective at removing rust from workpieces
The two key areas of heath risk associated with shot blasting are inhalation and the risk from debris. There are well established procedures that should always be followed to mitigate these risks and maximise worker safety, including safe working practices and PPE. Further details can be found in our Guide to Shot Blasting.
Shot blasting and sand blasting are often confused. The two treatments have similar methods of delivering the abrasive but use different materials. Shot blasting usually refers to an automatic wheel blast machine using metallic abrasive. Abrasive blasting, which is often referred to as sand blasting can use metallic or mineral abrasives and typically is delivered through a compressed air system with a manual operation. Sand as a blasting medium is now outlawed in many territories due to its danger to health.
Select the application type you’d like solutions for
{{ steps_labels.step_2.text }}
{{ steps_labels.step_3.text }}
{{ steps_labels.step_4.text }}
Contact our experienced sales team to discuss your requirements.
Contact